大林組とトヨタ自動車、炭素繊維強化プラスチック廃棄物をコンクリート材に 「リカボクリート™工法」開発
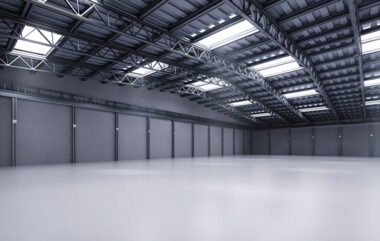
株式会社大林組(本社:東京都港区、社長:蓮輪賢治)とトヨタ自動車株式会社(本社:愛知県豊田市、社長:佐藤恒治)は共同で、燃料電池車「MIRAI」の水素タンクに使用されている炭素繊維強化プラスチック(CFRP)の端材を、コンクリート補強用短繊維(※1)として再生利用する新たな技術「リカボクリート™工法」(※2)を開発し、トヨタ明知工場内の部品置き場床面に初適用しました。
本技術により、CFRPの廃棄量を削減することができ、サーキュラーエコノミー(循環型経済)の推進に貢献します。
開発の背景
CFRPは、軽くて強度が高く、耐久性に優れることが特長で、水素を燃料とする燃料電池車の水素タンクや航空機、風力発電の風車ブレードなどに利用されています。
しかし、CFRPの性能を保ったままで再利用することは難しく、端材として発生したCFRPは電炉で鉄をリサイクルする工程での原料として使用するにとどまっています。そのため、CFRPが持つ強度を活かした利用ができていませんでした。
このたび、両社は共同で、仕様の検討や品質確認を積み重ね、コンクリート補強用短繊維として再生利用する新たな技術「リカボクリート工法」を開発しました。
本技術では、燃料電池車の水素タンクを製造する段階で発生するCFRPの端材に独自の熱加工を施し、適切な長さに裁断します。その後コンクリートに添加することで、コンクリートのひび割れ抑制や靭性の向上を実現します。
図1資源循環と開発技術の概要
写真1 施工状況 (炭素繊維カット材を投入)・写真2 施工状況 (リカボクリート打設)
本技術の特長
(1) 独自の熱加工により、CFRP端材表面層からCFRPをはがす技術を確立
CFRPの性能を保ったまま連続的にはがすことができ、コンクリート補強用短繊維への加工が容易になりました。
(2) ポリプロピレン製短繊維の3分の2の添加量で同等以上の性能を発揮
今回の再生加工したコンクリート補強用短繊維は、同じ目的で従来使われてきたポリプロピレン製短繊維の3分の2の添加量で同等以上の圧縮強度や曲げ靭性を発揮します。
図2 コンクリート部材の曲げ靭性試験結果(寸法:100×100×400㎜)
(3) CO2排出量を15分の1に低減
今回の再生加工したコンクリート補強用短繊維は、新品の炭素繊維と比べて、CO2排出量を15分の1に、通常の補強鉄筋の使用との比較では、9分の1にそれぞれ低減できます。
今後の展望
今後、燃料電池車の市場拡大に伴い、水素タンクの製造が増加することを見据え、両社は技術開発を継続し、さまざまなコンクリート構造物への適用を進めていきます。2026年度までに製造システムを実装して、年間3万m³の繊維補強コンクリートへの適用を目標とすることで、サーキュラーエコノミー(循環型経済)の推進に貢献します。
※1 コンクリート補強用短繊維
コンクリートと混ぜることで、靱性(粘り強さ)を高めることができる繊維質の補強材で、繊維の種類は、炭素繊維の他に鋼繊維、有機系繊維(ポリプロピレンやビニロン繊維等)などがあります。土木や建築分野で多くの使用実績があります
※2 リカボクリートは株式会社大林組の商標です